top of page
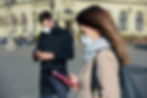
New Arrivals Are Here
About Us
From the moment we opened our doors in 2000, The Royal Luxury has been offering customers the best choices at unbeatable prices. Our brand encourages local manufacturing and the use of recycled materials whenever possible, and works hard to keep developing fine-quality products that last. Find all that you've been looking for—scroll through our vast selection today.

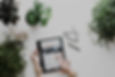
1 Year Warranty
Only the Best
This is your Feature description. Write a short blurb explaining what the feature is and why it matters for visitors, customers or clients. Don’t be afraid to toot your own horn! Take this opportunity to emphasize the important benefits or key advantages.
bottom of page